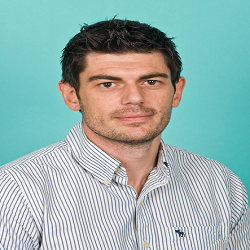
Professor Robert Kay
University of Leeds,
United Kingdom
BIOGRAPHY
I am a Professor of Advanced Manufacturing at the University of Leeds. I have been involved in manufacturing processes research both in academia and industry since 2001. My career started in the electronics manufacturing sector where during my PhD, I developed a novel microfabrication process which led me to create the spin-out company, MicroStencil Limited. During my 7-year period as Chief Technical Officer, I established a UK based production line alongside manufacturing partnerships in Asia and built a diverse customer base. In 2012 I started my 1st academic posting where my research involves using digital fabrication techniques such as 3D Printing to produce functional devices and products. I now have a range of funded projects in the field both looking at fundamental process developments and industry sponsored research. All of my work is multidisciplinary and involves collaborative teams from other universities, industry, research centres and medical professionals. My current research application areas include the manufacturing of bespoke and complex devices covering topics such as:
- Engineered ceramics
- Medical devices
- Wireless communications, sensor systems and electronic components
- Robotics and autonomous systems
ABSTRACT
Ceramic Hybrid Additive Manufacturing Platform (CHAMP)
Engineered ceramics are used across a diverse range of industrial sectors including electronics, healthcare, areospace, power generation, and aerospace. Conventional methods of ceramic manufacturing impose significant design constraints and require high-volume production to be economically viable. Significant attention has focused on using Additive Manufacturing processes to overcome these restrictions. However, barriers remain that limit the industrial adoption of 3D printed ceramics including process speed, range of processable materials, cost, porosity and part shrinkage
A new hybrid manufacturing approach that combines both additive, subtractive and layer drying processes within a single platform has the potential to overcome these limitations. This talk will cover the development of this technology from a machinery and material prospective and showcase ceramic demonstrators that highlight the advantages of this novel manufacturing technique. Furthermore, through the use of machine learning to monitor the hybrid manufacturing process this presentation will demonstrate the creation of defect-free ceramic components.
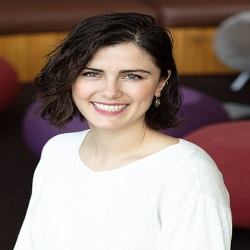
Dr Derya Baran
King Abdullah University of Science and Technology (KAUST),
Saudi Arabia
BIOGRAPHY
Prof. Derya Baran, originally from Turkey, received her BS and MS degrees from Chemistry Department at Middle East Technical University in 2008 and 2010, respectively and doctorate degree from Friedrich-Alexander Erlangen-Nürnberg University in Materials Science and Engineering in 2014. She then received the Helmholtz Association postdoc grant and pursued joint post-doctoral studies at Jülich Research Center (Germany) and Imperial Collage London (UK). Since January 2017, she is a faculty at King Abdullah University of Science and Technology (KAUST). As of 2021 she is an Associate professor in Material Science and Engineering Program. Her research group (OMEGALAB) focus on the engineering smart materials for printed energy harvesting applications and integrated electronics. She is selected for MIT Technology Review’s 2018 list of ‘35 Innovators under 35’ and selected as ‘Talented 12’ in Chemistry given by ACS C&EN. She is co-founder of two start-up companies. She strives to be a role model with her research and research ethics to younger generations. She is a member of Global Young Academy since 2020.
ABSTRACT
Functional Materials for Printed and Stretchable Electronics
The field of printed and stretchable electronics has witnessed remarkable advancements, propelled by the development of functional materials. N-type organic semiconductors exhibit electron mobility, crucial for creating efficient electronic devices. Their integration into printed electronics enhances flexibility and enables the fabrication of intricate circuits on diverse substrates. Concurrently, conductive composites play a vital role in achieving stretchability, allowing electronic components to conform to curved or irregular surfaces. This talk encapsulates the pivotal role of these materials in pushing the boundaries of electronic design and tactile sensing paving the way for innovative applications in wearable technology, healthcare, and beyond.
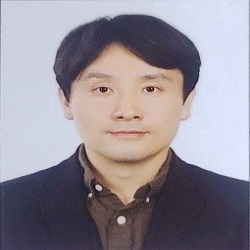
Professor Jang-Ung Park
Yonsei University, Seoul, Yonsei-IBS Institute,
Republic of Korea
BIOGRAPHY
Jang-Ung Park achieved his Ph.D. degree from the University of Illinois at Urbana-Champaign (UIUC) in 2009. After that, he served as postdoctoral fellow at Harvard University from 2009 to 2010. He worked as an assistant / associate professor in School of Materials Science and Engineering at UNIST from 2010 to 2018. He is now a professor in the Department of Materials Science and Engineering at Yonsei University and the Department of Neurosurgery at Yonsei University College of Medicine. His current research is focused on wearable and biomedical electronics.
ABSTRACT
High-resolution 3D Printing of Liquid Metals for Neural Interface Electronics
Recent progress in optoelectronic devices for wearable electronics demands their outstanding mechanical deformability for versatile systems in daily life. Especially, Rapid advances in neurotechnology enable bidirectional communication between the nervous system and engineered devices. The precise recording and stimulation of typical target neurons by neural interfaces with adequate materials and structures can provide revolutionized medical applications, including the diagnosis and treatment of neurological disorders. Thereby, a proper understanding of the electronic device and its interfacing biological surroundings is necessary. Here, this talk presents the fundamental concepts of neural signaling, neural recording, and stimulation to introduce neural interfaces with wearable electronic devices. Then, we summarize the considerations of the materials and introduce a variety of materials that satisfy the requirements. Furthermore, the key challenges for next-generation neural interfaces are considered, and future directions are explored based on recent studies.
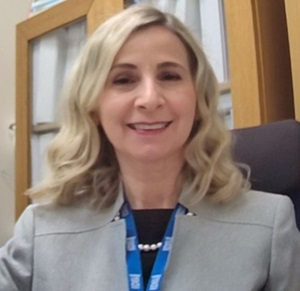
Ms Vesna Covic Palikuca
University of Doha for Science and Technology,
Qatar
BIOGRAPHY
Vesna Covic Palikuca has been working for UDST as a lecturer/mechanical instructor for the past 11 years. Hailing from Canada, Vesna holds the title of Professional Engineer, bringing over 15 years of industrial expertise in designing heavy machinery and downstream equipment for the oil and gas sector. Vesna's job as a senior mechanical engineer was related to the design, prototyping and testing of fibreglass reinforced pressure vessels for CNG application, high-pressure piping design structural frames, corner castings industrial burner design, etc. Vesna has been passionate about teaching engineering courses in engineering mechanics, 3D design, materials, and maintenance courses. Additionally, she serves as a technical advisor for numerous capstone and research projects. Vesna has been actively involved in the establishment of UDST's Additive Manufacturing Center and specializes in Fused Deposition Modeling (FDM), Stereolithography (SLA), and metal Fused Filament Fabrication (FFF) processes. Vesna continuously shared her enthusiasm for educational science and innovative teaching methodologies, particularly in constructivist learning. She shared the role as an active speaker at various conferences, professional development days and workshops, expressing her dedication to advancing engineering education.
ABSTRACT
Smart Manufacturing in Experiential Learning at UDST
Experiential learning has been an integral teaching methodology at UDST for more than 20 years. 3D printing has been successfully embedded into our engineering programs in recent years, while fully supporting our experiential learning methodologies. In our classroom, we see the application of different 3D printing technologies as an integral part of the course delivery, based on hands-on and applied to learning.
To enrich the profile of UDST in 3D printing and other digital manufacturing technologies the university has introduced a new B.Sc. program in Smart Manufacturing unique to the region and covers key areas of additive manufacturing, subtractive manufacturing and other automated manufacturing processes and materials essential for the knowledge toolbox of our graduates to feed to the national, regional and global workforce.
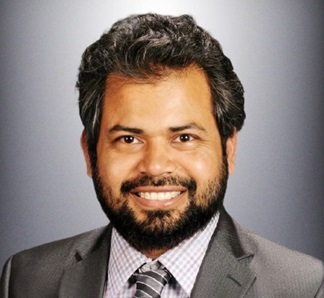
Dr. Kunal Mondal
Fusion and Fission Energy and Science Directorate at Oak Ridge National Laboratory and Idaho State University,
United States of America
BIOGRAPHY
Dr. Kunal Mondal serves as a nuclear materials scientist in the Fusion and Fission Energy and Science Directorate at Oak Ridge National Laboratory and affiliate and Allied Graduate faculty to the Idaho State University. His focus centers on meticulous material examinations, particularly those tailored for extreme environments, spanning additive manufacturing, micro/nano fabrication of functional materials, liquid metal, photovoltaics, polymer thin-films, carbon nanomaterials, energy, environmental health sensors, and nuclear sensors. Dr. Mondal holds a doctoral degree in Chemical Engineering from the esteemed Indian Institute of Technology, Kanpur, complemented by master's degrees in Materials Engineering and Applied Physics with a Nuclear Physics specialization. His academic journey also includes a bachelor's degree in physics from the University of Burdwan.
Before joining Oak Ridge National Laboratory in 2023, Dr. Mondal served as a Staff Scientist at the Idaho National Laboratory, contributing significantly to the field. His postdoctoral research encompasses the Department of Chemical Engineering at North Carolina State University and a teaching and research role in robotics and actuators at Florida Atlantic University's Department of Mechanical Engineering. Since 2020, he has held an affiliate and allied graduate faculty position at Idaho State University's Civil and Environmental Engineering Department. Dr. Mondal's wealth of experience and diverse research interests position him as a valuable asset in advancing nuclear materials science and its varied applications.
ABSTRACT
Advanced manufacturing for nuclear sensor and harsh environmental applications
This study probes into the integration of cutting-edge manufacturing methods, additive processes, and microfabrication techniques for crafting nuclear sensors designed for use in extreme environments. Key features include the use of radiation-resistant materials, 3D printing for compact sensor design, and the integration of digital twins and artificial intelligence for data interpretation. An illustrative example highlights an additive manufactured nuclear melt wire sensor measuring reactor temperature, showcasing collaborative advancements in challenging environments. The study outlines the development of miniaturized melt wire chips through additive manufacturing, specifically tailored for in-pile use within reactors and addressing spatial constraints. These compact sensors, proficient at sensing specific temperature ranges, exhibit resilience in irradiating testing conditions. Additionally, the study reports on the fabrication of high-temperature-tolerant and radiation-resistant silicon carbide (SiC) nanowire Schottky diodes. Dispersed in liquid solvents, these nanowires offer a solution for deploying electronics in harsh radiation environments. The sensors display stable performance, even under proton irradiation, suggesting their potential for use in solution-processable electronics for extreme conditions, ensuring radiation measurement and nuclear safety and security in a broad application spectrum.
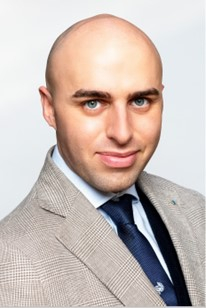
Mr Riccardo Nicastro
Caracol AM
Italy
BIOGRAPHY
Riccardo is a multilingual performance driven Executive focused on Advanced Manufacturing, Industry 4.0 technologies and food industry with international experience in multinational consulting and industrial institutions. Riccardo has held management roles with increasing responsibilities delivering global-scale programs. His technical background in mechanical engineering has been enriched to broader matters through a Global Top 3 Executive MBA (FT 2023).
Riccardo is Group Chief Commercial Officer for Caracol. In addition to this role, Riccardo is:
- General Manager at Caracol Middle East
- Co-Founder & CEO at NIRI
- Co-Founder & General Manager at Dalnic Consulting
- Managing Partner at Enrietto
Riccardo is member and founder of diverse no profit and volunteering associations. Husband and father.
ABSTRACT
Producing renewable energy parts from recycled wind turbines with Large Format 3D Printing technologies
Caracol has been working to demonstrate how to use digital green technology to create new industrial value chains achieving waste valorization.
Specifically using recycled glass fiber from disused wind turbines the company and its partners aim to effectively produce new, renewable energy applications implementing circular economy loops in advanced manufacturing supply chains and fostering the development and use of more sustainable production technologies.
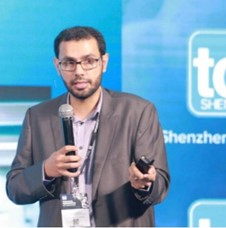
Dr Ehab Saleh
University of Doha for Science and Technology,
Qatar
Workshop technical chair
BIOGRAPHY
For the past nine years Dr Saleh has worked on developing digital manufacturing processes for the fourth industrial revolution (IR4.0) utilizing multi-materials to form integrated 3D structures containing metals, polymers and glasses. He is currently an Assistant Professor in Smart Manufacturing at the University of Doha for Science and Technology (UDST) and the Program Lead of its B.Sc degree in Smart Manufacturing program.
Dr Saleh’s current research activities span across multi-disciplines including the development of manufacturing processes for printed electronics and energy harvesting/storage applications, 3D printing of RF metamaterials and THz components, bio-printing using medical-grade materials and digitally manufactured controlled release pharmaceutics. He is regularly invited to deliver keynote talks on digital manufacturing in international events such as the IEEE Workshop on Functional Additive Manufacturing in Tokyo - Japan, CoInnovate Flagship in Cardiff – United Kingdom and TCT Summit in Shenzhen - China.
ABSTRACT
UDST portfolio of 3D printing research towards applied technologies
UDST has made key investments in its 3D printing portfolio recently to enhance the workforce expertise and the set of digital manufacturing equipment available for research activities to support its regional position in the development of cutting-edge 3D printing technologies.
In this portfolio showcase, Dr Saleh will go through the set of tools available within UDST premises to support research activities from different departments within the college of engineering and technology (CET) at UDST. This will include an overview of research advancements by UDST experts in 3D printing for various applications including 3D printed catalytical structures, 3D printed radio frequency and THz components, 3D printed pharmaceutics and other multidisciplinary 3D printed applications.